Numerical modelling and simulation of the combustion processes taking place in the gas-turbine combustion system are mainly performed by two project partners, SINTEF Energy and CERFACS. While SINTEF’s aim is to predict flame stabilization in the second combustion stage, where hydrogen combustion is mainly governed by autoignition, CERFACS focuses on the numerical modelling of the first combustion stage where the stability is controlled by flame propagation. This element plays a crucial role to leverage sequential combustion capabilities, in particular the possibility to run with any blends of natural gas and hydrogen, all the way to pure hydrogen. The advanced modelling capabilities will ensure flashback free operation and flame stability of the combustion system, while keeping low emissions.
In earlier collaborations with Ansaldo Energia, both companies explored the fundamental properties of autoignition-controlled hydrogen premixed flames using model-free direct numerical simulation (DNS). They apply now this expertise to more practical cases, advancing their understanding and enhancing the performance of hydrogen combustion system.
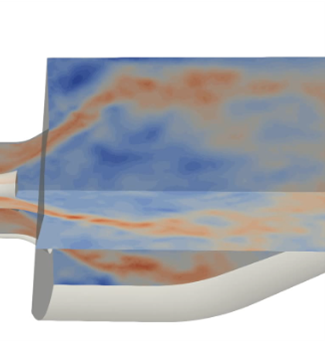
Both project partners use simulation methods that are quite unique for the FLEX4H2 project. SINTEF’s numerical modelling approach utilizes high-resolution Large-Eddy Simulation (LES) with a standard subgrid-scale combustion model and well-established chemical kinetics for hydrogen-air combustion. To address potential shortcomings of LES-based models in predicting the turbulent burning rate of hydrogen premixed combustion, they use a computationally expensive approach that combines high spatial and temporal resolution with the highest available formal accuracy of the numerical method. This “brute-force” strategy requires massively parallel execution of numerical simulations that use High Performance Computing (HPC) facilities and specialized software tools. Such advanced facilities and the expertise to perform HPC calculations at the necessary scale are typically out of reach for most industry players.
CERFACS’ simulation tool named AVBP relies on the Large-Eddy Simulation approach, too. In such simulation codes dedicated to complex geometries and complex reacting flow predictions, the fully unsteady process behind the operation of a combustor gas turbine is simulated in time and space including the chemical processes taking place in the flame front. All these phenomena are, however, very complex and for accuracy necessitate the use of super computers whereby using at once thousands of computing processes available on world class computers from national or international computing centres. Despite its cost, this approach, for which CERFACS’ team is a recognized worldwide leader, has shown unprecedented capabilities surpassing existing/conventional approaches. Adaptation to hydrogen combustion is nonetheless required and FLEX4H2 is a valuable vehicle to demonstrate such a tool capability for real and highly demanding industrial applications.
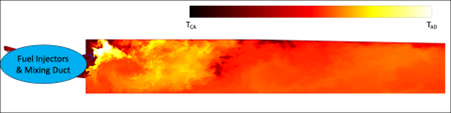